Preventive vs. Reactive Commercial Asphalt Maintenance: A Cost-Benefit Analysis for Facility Budgets
- Kevin Gray
- Feb 28
- 2 min read

As a facility manager, ensuring the longevity and safety of your property’s asphalt surfaces is crucial. One of the most common challenges is deciding between preventive maintenance and reactive maintenance. This blog will break down the cost-benefit analysis of these two approaches, helping you make informed decisions to protect your budget and extend the lifespan of your pavement.
What Is Preventive Asphalt Maintenance?
Preventive maintenance involves proactive measures to address minor issues before they escalate into expensive repairs. Common preventive strategies include:
Crack Sealing: Filling small cracks to prevent water infiltration and structural damage.
Sealcoating: Applying a protective layer to shield asphalt from UV rays, chemicals, and water.
Regular Inspections: Identifying early signs of wear and tear to address them promptly.
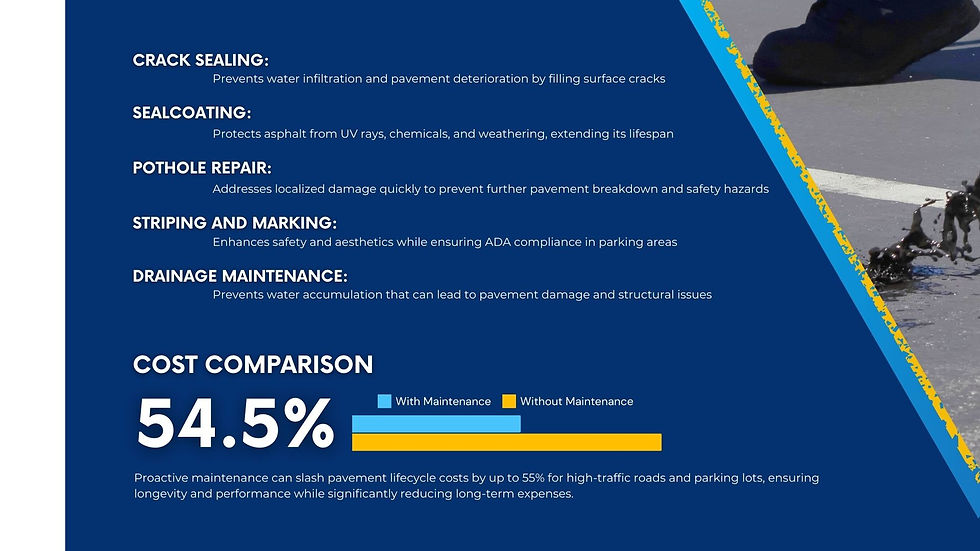
Benefits of Preventive Maintenance
Cost Savings: Preventive maintenance typically costs three times less than reactive repairs. For example, crack sealing costs $0.50–$3 per linear foot, while repairing potholes caused by neglected cracks can cost $100–$400 each.
Extended Pavement Lifespan: Sealcoating can add 5–7 years to the life of your asphalt, delaying costly reconstruction projects.
Improved Safety: Well-maintained surfaces reduce liability risks from accidents caused by potholes or uneven pavement.
Minimized Downtime: Proactive care reduces emergency repairs that disrupt operations.
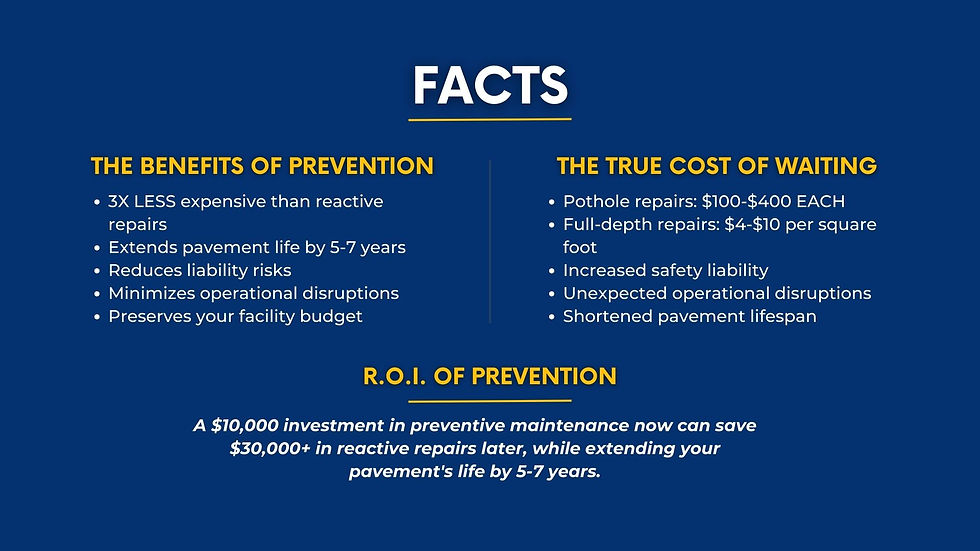
What Is Reactive Asphalt Maintenance?
Reactive maintenance involves addressing issues only after they occur, such as patching potholes or resurfacing damaged areas. While it may seem cost-effective in the short term, it often leads to higher expenses over time due to escalating damage.
Drawbacks of Reactive Maintenance
Higher Long-Term Costs: Neglected cracks can expand into potholes, requiring full-depth repairs costing $4–$10 per square foot compared to $1–$3 for resurfacing.
Safety Risks: Delayed repairs increase the likelihood of accidents, leading to potential lawsuits or insurance claims. Check out Common Signs Your Asphalt Needs Repair for tips on identifying issues early.
Operational Disruptions: Emergency fixes often require immediate attention, disrupting facility operations.
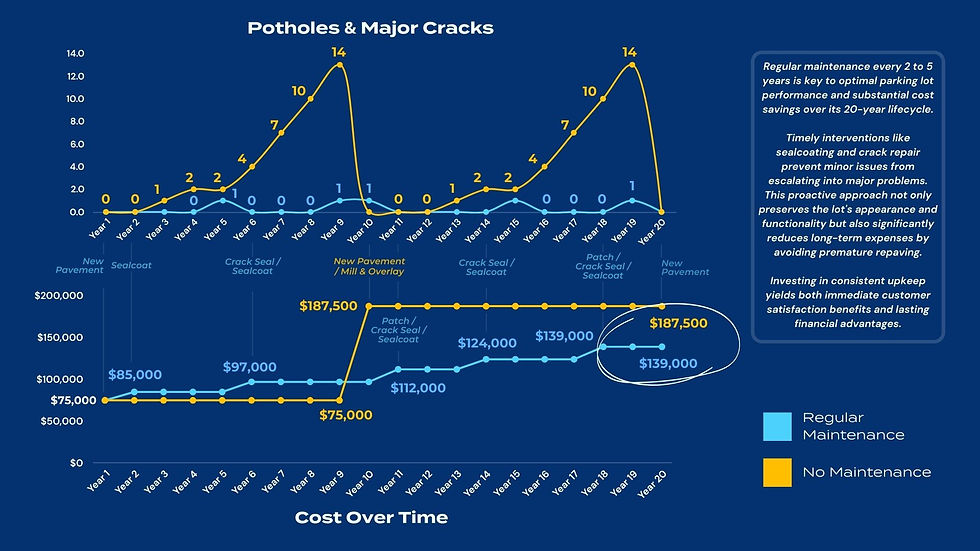
Cost Comparison: Preventive vs. Reactive Maintenance
Maintenance Type | Average Cost | Lifespan Extension | Key Benefits |
Crack Sealing | $0.50–$3/linear foot | 3–5 years | Prevents water infiltration |
Sealcoating | $0.25–$0.50/sq ft | 5–7 years | Protects against UV & chemicals |
Pothole Patching | $100–$400 each | Temporary | Fixes immediate safety concerns |
Full Replacement | $4–$10/sq ft | 15–20 years | Restores structural integrity |
Preventive measures like crack sealing and sealcoating are significantly less expensive than reactive solutions such as full-depth replacement or resurfacing.
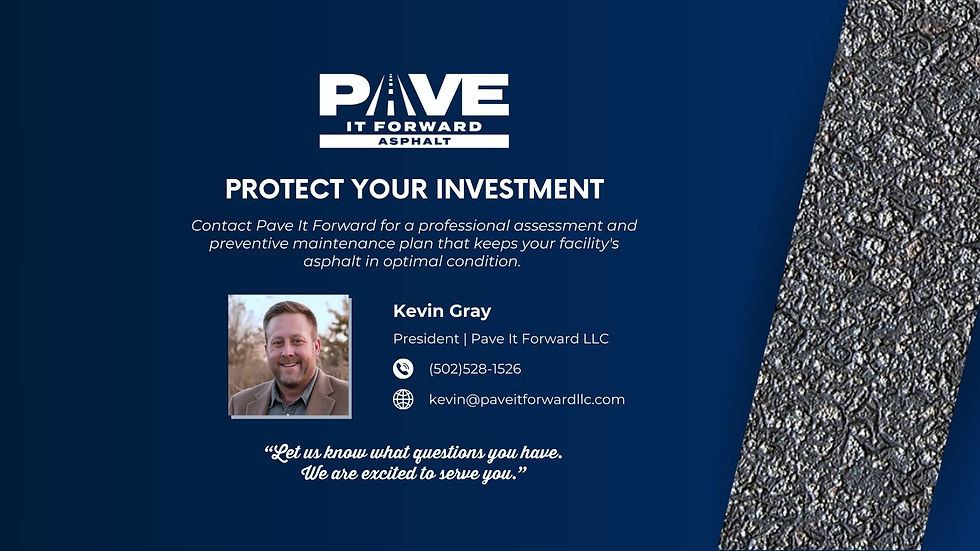
Why Preventive Maintenance Is the Smart Choice
Investing in preventive maintenance offers long-term savings, enhanced safety, and reduced operational disruptions for your facility. By addressing minor issues early, you can extend the lifespan of your asphalt while avoiding costly repairs down the road.
Want to learn more about Commercial Asphalt Paving? Check out our informational slide deck here!
Have a question or want to contact us? Click here to send us a message!
Kevin Gray
Founder and Owner, Pave It Forward Asphalt